Plug Valve Vs. Ball Valve: What are the Differences?
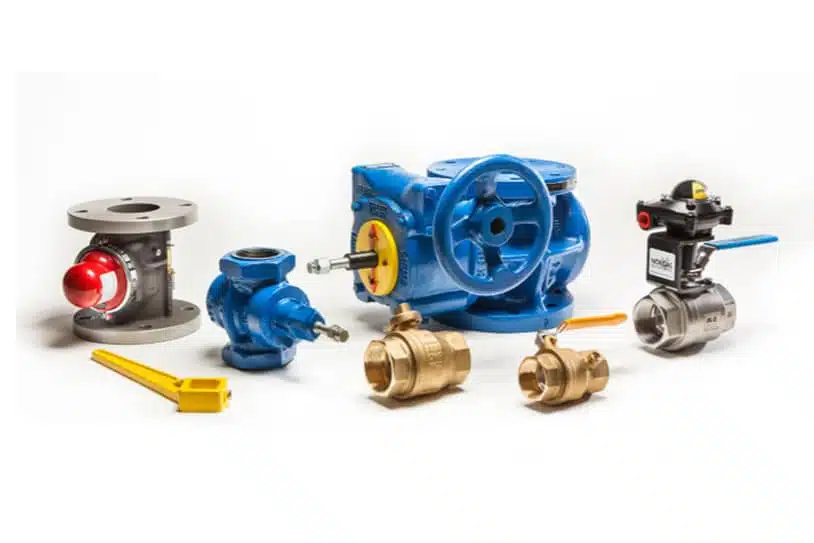
Control valves are an integral aspect of any production setup where you need to monitor, control or manipulate the flow of a fluid medium through a variety of piping areas of a system. Control valves come in two types – plug valves and ball valves. Even though there are some differences in their overall structure and functioning, both valves are quite similar in their overall purpose and are often used interchangeably in many applications.
Key Features of Plug Valve and Ball Valve
Whether it is oil and gas, chemicals, petroleum refining, wastewater and sewage, or even food and beverage industries, control valves have a wide range of applications across a number of different industries. Choosing the right type of control valve is critical in ensuring the safety and efficiency of your systems. Hence, it is important to understand their structure, functionalities, and other aspects, such as cost and maintenance.
1. Structure
Here’s a closer look at the two types of control valves:
Plug Valves
Featuring a conical tapered or a cylindrical disc, a plug valve controls fluid movement through one or more passages that go sideways through the plug. When the valve is open, the hollow passage aligns with the flow, allowing the fluid to flow freely. A 90-degree rotation closes the valve and realigns the plug to block the flow.
Used for cutting, distributing, or changing the flow of media, the plug valve is small and simple. Its main applications are in medium or low-pressure, low-temperature settings, although certain specific types of plug valves can work in high-temperature settings as well.
Besides two-way, three-way or multi-point port openings, gas plug valves are available in four different styles, including lubricated, non-lubricated, expandable, and eccentric.
Learn more about plug valves here: What is a Plug Valve and What is it Used for?
Ball Valves
A modified version of the original plug valve, the ball valve features a spherical disc and a circular bored passageway. The disc has a hole in it, called the port. When the port aligns with both ends of the valve, the valve is open and the medium flows through it. When the port is perpendicular to the ends of the valve, the flow stops.
With a compact structure, easy operations and maintenance, and compatibility with water, natural gas, acids, and solvents, ball valves are suitable for a variety of systems. Ball valves are a good fit even for the working conditions of harsh media, such as hydrogen peroxide, methane, ethylene, or oxygen. While traditional gas shutoff ball valves are most suitable for an open and close functionality, the more advanced or customized versions provide flow control, as well as throttling capabilities.
Ball valves come in four different types of construction:
- Full port or full bore ball valve features an oversized ball, in which the hole and pipeline size are the same, resulting in lower friction loss. As the valve is more expensive and larger in size, it is usually used only where free flow is necessary, such as pipelines that require pigging.
- Reduced bore ball valves include a ball that is slightly smaller than the valve’s pipe size. This makes the flow area smaller, and in turn, increases the velocity of the flow.
- A V-port ball valve, which features a v-shaped ball, enables a more controlled opening and closing of the orifice to achieve a near linear flow.
- A trunnion ball valve features additional mechanical anchoring that supports the ball or disc between the stem and the shaft. This type of ball valve is useful in applications that need higher pressure or larger valves.
2. Function
Both plug valves and ball valves are quarter-turn valves that open and shut with a quick 90-degree turn of the actuator. Their primary use is for sealing and shut-off operations. However, the sealing surface of the plug valve is significantly larger than that of a ball valve. While this translates to better sealing qualities, it also means greater torque and more effort in operation.
Due to their torque-free operation and light weight, ball valves are relatively easier to operate than plug valves. Although their smaller sealing surface could mean low sealing performance, advancements in seal injections and chemical sealants have helped in addressing this shortcoming.
3. Maintenance
Both types of control valves need regular maintenance to function efficiently. Plug valves are relatively easier to maintain as they have a simple construct and not many moving parts. Moreover, you can remove and clean the plug and also easily access the rest of the valve body for hassle-free cleaning.
Ball valves are tougher to clean as the ball or disc sits deep inside the valve, making access difficult. Over time, the body cavity of the ball valve may accumulate particles from the medium which further adds to its cleaning and maintenance hassles.
Overall, plug valves offer low-cost operations, as compared with ball valves. This is because in the plug valve, the plug fits under the bushing, which keeps the valve body and plug free from wear. Simply replacing the bushing and top seal is sufficient for updating and maintaining the valve’s optimum function and long-term service requirements.
4. Application
The larger surface and unrestricted flow enabled by plug valves makes them ideal for applications that involve mud, slurries or sewage. Fortified plug valves provide tight seals while dealing with hard or corrosive mediums. Their simple structures, ease of operations and maintenance, and anti-corrosion qualities make them a reliable shutoff option for most critical applications.
The versatile ball valves are a popular choice for a variety of automated applications, including gas feed lines, crude oil, LNG, field gas or polymer plants, turbine, compressor or separator skids, tank farms, oil refinery feedstock lines, hydrocarbon processing, and more. While stainless steel ball valves are suitable for cooling water, petroleum refining, feed water, brewing and desalination, high-pressure ball valves are an excellent choice for underground, subsea, and cryogenic services.
Choose the Right Type of Control Valves for Your Application
The purpose of ball valves and plug valves is to offer greater control. They are, in fact, called control valves for this reason as they ensure the ideal seals for various industrial applications. It’s important to recognize the differences and capabilities to choose the correct valve.
While more expensive and heavier for operations on a larger scale, plug valves rank higher on their tight sealing capabilities. It is true, however, that they are not easy to operate. When you have a larger application that requires easier operation, ball valves are a better choice. Keep in mind though, that their sealing capabilities are not as tight as plug valves. To improve the sealing ability of a ball valve for your large-scale application, you may need additional technology and updated mechanisms.
At Norgas Controls, our team of specialists can help you choose the right type of gas plug valves or ball valves for your application, including custom solutions based on your specific project requirements. We also offer gas regulators and gas measurement solutions such as Romet rotary gas meters. Feel free to contact us for any specific requirements you might have.
Additional readings: